High-performance, compatible implants
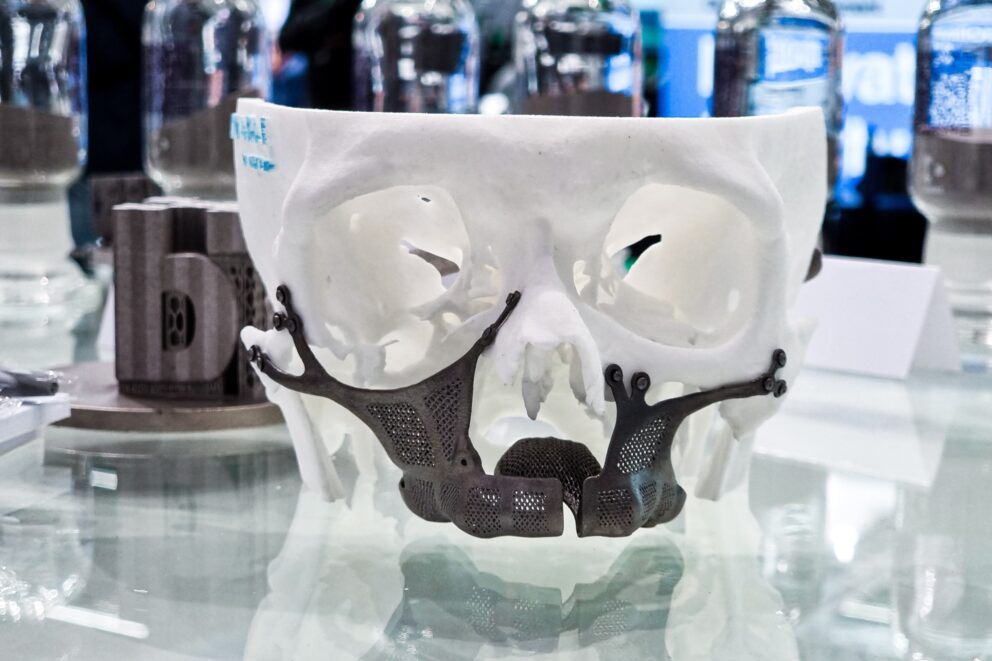
Tantalum and niobium revolutionize 3D printing in medical engineering
Medical implants are gaining in importance for patient quality of life. Advancements in additive manufacturing processes, otherwise known as 3D printing, and the development of compatible tantalum and niobium alloys offer highly promising approaches for manufacturing customized, biocompatible implants. These two materials are defining the direction of modern medical engineering: Optimal performance combined with maximum customization.
Author: Markus Weinmann, Lead Scientist for Technology Scouting and Business Development at TANIOBIS GmbH
Medical implants play a decisive role in modern medicine and are essential for barrier-free living. Implants improve quality of life in this regard and help sustain life by maintaining or even restoring physical functions. Irrespective of whether they are exceptionally large or microscopically small and even extremely durable, above all, implants need to be biocompatible. If this is not the case, there is a risk of inflammation, and the body will reject the implant. Implants produced using 3D printing can fulfill these requirements, depending on the material used.
Tantalum and niobium alloys: Biocompatible alternatives
Implants come in many types and serve diverse purposes: We make a distinction between dental implants, orthopedic implants, such as joint prostheses or spinal implants, and functional implants, such as those in the inner ear. Each implant must be tailored to the specific patient and their body. Ti-6Al-4V alloys, composed of titanium, aluminum, and vanadium, are currently the most commonly used alloys in orthopedic and dental implants. Over 90 percent of all dental and bone implants are made of this material or pure titanium. This is mainly because the alloy is exceptionally strong and provides excellent corrosion resistance. However, many people’s bodies reject this alloy; about 20 percent of patients treated are unable to tolerate these implants. This leads to infections and inflammations in the individuals concerned, possibly requiring the implant to be removed. Titanium, tantalum, and niobium alloys are much more compatible alternatives. By forming a dense oxide layer on their surface, they create a biocompatible material which is exceptionally strong, ductile, and elastic. As a result, the properties of these alloys closely resemble those of bone. Moreover, additive manufacturing makes it possible to manufacture complex, compatible implants made of tantalum and niobium alloys which can be customized to the patient’s requirements.
Medical advancement thanks to 3D printing
3D printing offers a combination between fast production and individual customization. This, in turn, enables rapid technological advancements in research and development as well as in medical technology production. The use of tantalum and niobium materials seems to be highly beneficial in these areas. They have high melting points and withstand temperatures of over 3,000 degrees Celsius. This makes it extremely challenging to use conventional machining methods like casting. However, 3D printing offers numerous ways to shape and customize materials.
Specially developed tantalum and niobium powders can be used in additive manufacturing to produce components which not only withstand high temperatures and offer excellent mechanical properties, but they provide effective resistance to corrosion and oxidization while also being highly biocompatible. Amtrinsic® powders by TANIOBIS comprise spherical, gas-atomized, tantalum- and niobium-based alloy powders with machining properties specially developed for 3D printing. They are suitable for all widely used additive manufacturing technologies – from Laser Beam Powder Bed Fusion (LB-PBF), Electron Beam Powder Bed Fusion (EB-PBF) to Directed Energy Deposition (DED). Customization and adaptability are priorities here, especially in biomedical applications.
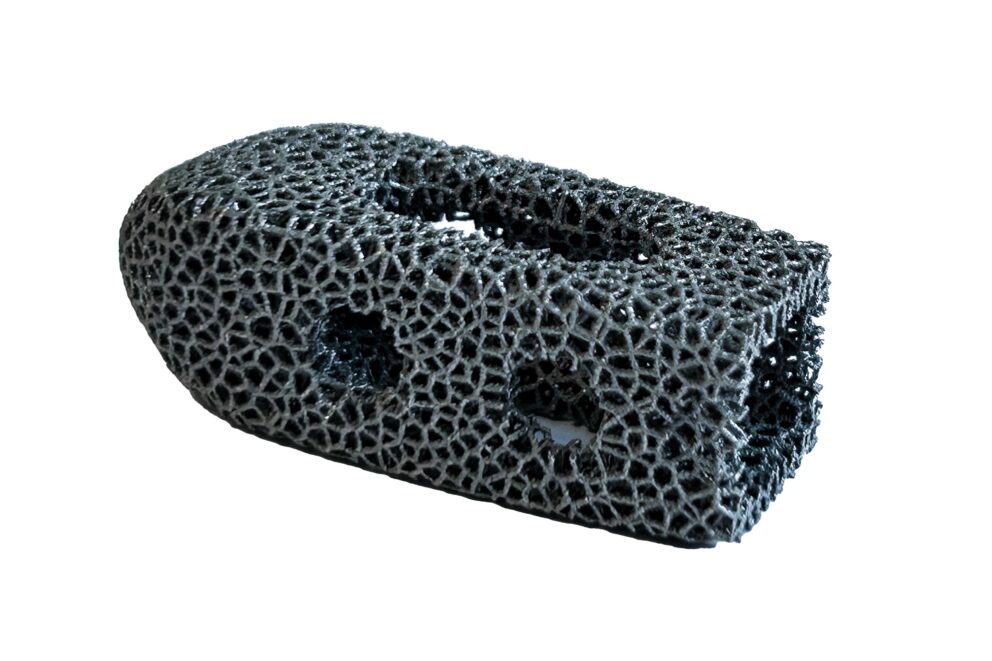
Customization in medical engineering
The healthcare sector is moving towards increasingly greater personalization for patient treatment with regard to both therapeutic practices and medical products. Alloy powders based on titanium, niobium, and tantalum are leading the current trend in medical engineering as it moves towards smaller, lighter, yet more powerful and personalized medical products. However, tantalum and niobium powders are not only in demand in medical engineering. Their property profile makes them particularly appealing for applications in the aerospace industry and for superconductors fitted into quantum computers. Niobium and tantalum powders are not only revolutionizing 3D printing but are also paving the way for megatrends.