TANIOBIS: Powders that push the limits
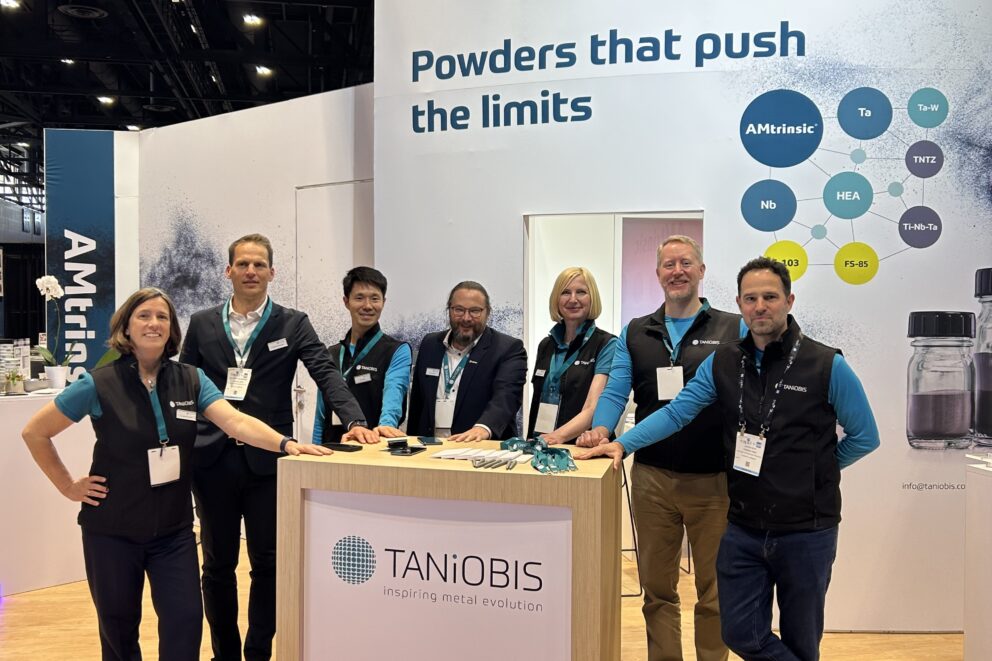
How AMtrinsic® tantalum and niobium powders have been redefining the boundaries of 3D printing for five years
TANIOBIS produces premium materials, powders and alloys based on tantalum and niobium. In addition to having an impact on global technology trends such as AI and big data with these materials, TANIOBIS is tapping into another megatrend with its metal powder AMtrinsic®. These powders have been a key integral part of additive manufacturing for the past five years. In an interview, Katarzyna Kosowski, Head of Corporate Communications, and Stefan Richardt, Technical Sales Manager Additive Manufacturing, explain what the brand represents and how it managed to secure its place in the market.
AMtrinsic® has now been on the market for five years. Why is the brand so successful? What sets it apart?
Katarzyna Kosowski: The combination of the versatile characteristics of the spherical, gas-atomized, tantalum- and niobium-based alloys and the creative freedom of additive manufacturing technologies opens up new possibilities for users from the outset. The main areas of use for AMtrinsic® are medical implant printing, manufacturing of heat- and corrosion-resistant components in the chemicals industry, and high-temperature applications in the aerospace industry, all highly future-oriented sectors.
Stefan Richardt: We established an extensive academic network for development years ago, which includes Hannover Medical School (MHH), the Lower Saxony Center for Biomedical Engineering, Implant Research, and Development (NIFE), and the Orthopedic Clinic at the University of Rostock Hospital. Moreover, we have also maintained and continue to maintain ongoing contact with our clients and partners, who affirm the current interest in titanium alloys enhanced by the addition of the intrinsic properties of niobium and tantalum.
Katarzyna Kosowski: Interestingly, ‘intrinsic’ was also the key word we used in our search for a brand name. AMtrinsic® is composed of two parts: AM stands for additive manufacturing while ‘trinsic’ comes from ‘intrinsic properties’.
What new capabilities can users achieve with AMtrinsic®? Do you have any examples?
Stefan Richardt: The materials tantalum and niobium have high melting points, i.e. they do not melt until they reach temperatures of over 3,000 degrees Celsius. This means they cannot be cast and are difficult to process using conventional methods. 3D printing, on the other hand, offers a wealth of possibilities for shaping and renders both materials malleable. AMtrinsic® powders open up entirely new worlds for additive processing. It can be used to print components capable of withstanding even extremely high temperatures. There is also another advantage: Additive manufacturing produces hardly any material waste, unlike subtractive manufacturing methods such as milling, eroding and grinding.
In what specific areas is AMtrinsic® used today?
Stefan Richardt: TANIOBIS is active with AMtrinsic® in virtually all branches of industry with the aerospace sector being one example. Our clients in this industry use it to manufacture thrusters which help to reposition satellites or change their orbit. The high temperature resistance in tantalum and niobium alloys increases the lifespan for thrusters and, consequently, the useful life for satellites. The chemical industry also benefits from these material properties. Tantalum’s high corrosion resistance protects valves which need to convey all types of acids and alkali solutions. In medical engineering, the combination between tantalum and niobium is particularly suitable for manufacturing implants thanks to their optimum biocompatibility. An alloy made of tantalum and niobium combined with titanium materials makes an excellent biocompatible material which is ductile and thus able to closely mimic the characteristics of bones. As a result, our clients are already successfully manufacturing spine implants with it, offering an extremely compatible alternative to the more commonly used titanium 64 alloys (with aluminum and vanadium), which are not as biocompatible.
How long did it take to bring the product from development to market launch? What were the greatest challenges?
Stefan Richardt: Processing the powder was a tough technological task for our research and development team as it was unknown whether the high melting points of our materials would be compatible with 3D printing technology.
We have been building up an exceptionally good working relationship with the Hannover Laser Center (LZH) since 2015 and pooled our expertise with theirs extensively for this project. Our regular EB and SPT powders were used at first, but we then also included our AMtrinsic powder.
Katarzyna Kosowski: Such processes take time. Several years passed before the market launch in October 2019. Since the beginning of this process, alloy powder development has taken place at our main location in Goslar..
What direction do you foresee for your innovative products and developments moving forward?
Stefan Richardt: Our powders’ characteristics are extremely appealing for certain end applications such as super conductors, medical implants, or applications in the aerospace industry, i.e. the current megatrends. That’s why I’m sure that these fields will remain relevant or even gain in importance in the future. The demand is high for special alloys and AMtrinsic powders specific for the newly developing innovations on the 3D printing market. TANIOBIS is well-equipped to meet this demand.
Katarzyna Kosowski: The range of trade fairs, conferences, publications, and digital platforms is considerable in the 3D printing market, for example. These channels also give us the platform to share our visions. The ongoing dialog and efficient working relationship between departments and within the sector are fundamental components for ensuring a sustainable communication framework, an area where we’re already excelling and will keep pushing forward.
What steps did you take to make sure the AMtrinsic® brand became effectively and conclusively positioned in the market?
Katarzyna Kosowski: First, we obviously pursued conventional routes. This included running campaigns in trade publications and placing ads. But we’re also increasingly connecting with our audience on social media, especially on Instagram and LinkedIn. Highlights during the AMtrinsic® campaign included participation in additive manufacturing trade fairs, such as Formnext in Germany. We also took our brand to international trade fairs such as Rapid/TCT in the US. When launching a product onto the market, it’s crucial to closely examine what particularly unique selling features our product has compared to the competition and how we communicate these. This part of the process is known as “Brand Identity Development”. Moreover, the brand needs to be reviewed and protected from a legal standpoint before being presented through the right marketing channels to build its presence. We then developed the brand name and the logo based on the defined brand values.
Stefan Richardt: This also includes the claim Powders that push the limits, which perfectly encapsulates the message that our brand conveys. It underscores the fact that creating complex geometries in 3D printing combined with the unique intrinsic characteristics of our AMtrinsic® powder unlocks opportunities for entirely new applications and addresses each task with full dedication.